◇ TPM 的定义:
T.P.M (Total Productive Maintenance)
1. T (Total)
包括生产部门的开发、营业、管理等公司内的全体部门全員參加(人、物)
2. P (Productive)
包括生产、教育、销售等制造效益的所有业务
3. M (Maintenance)
面向生产SYSTEM的LIFE CYCLE全体.效率的极限追求为目的,生产体系维持
理想状态的活动。
◇ TPM的释义:
1. 追求生产系统效率 (综合效率)的极限,以改善企业体质为目标。
2. 在现场、现物架构下, 以生产System生命周期为对象,追求灾害”0”、
不良“0”、故障“0”浪费“0”等,并将所有损失在事先加以防止。
3. 除生产部门外,还包括开发、销售、管理等所有部门
4. 从最高经营者到现场一线员工的全员参与的活动
5. 依靠小集团活动的,达成 Loss Zer"o"化的目标.
◇ TPM的历史背景:
[ 从美国式的PM到日本式的 TPM ]
事后保全:B.M(Breakdown Maintenance) 1960年代以前
↓
预防保全:P.M(Preventive Maintenance)
↓
改良保全:C.M(Corrective Maintenance) 1970年代
↓
保全预防:M.P(Maintenance Prevention)
↓
生产保全:P.M(Productive Maintenance) 1980年代至今
↓
综合PM: TPM(Total Productive Maintenance)
◇ TPM 的思想:
1. 全员参与的小集团活动思想
2. 预防思想
3. “0”化思想
◇ TPM 的方针:
- 全员专家 浪费“0”化 挑战极限
◇ TPM 的目的(双赢策略):
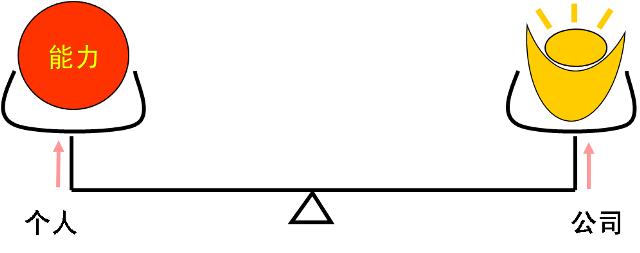
个人能力及公司综合效率提高!
◇ TPM 的目标:
●灾害“0”化 ●故障“0”化
●不良“0”化 ●浪费“0”化
◇ TPM 的成果:
推行TPM不仅可以使企业充分发挥设备的生产潜力,获得良好的经济
效益和广告效应,而且可以使工厂环境和员工精神面貌发生巨大的变
化,企业树立起良好的社会形象。如,日本西尾泵厂TPM推行之后,
做到了无故障停机,100万件产品仅发生11件次品,西尾泵厂被誉为
"客厅工厂"。日本尼桑汽车公司在最初推行TPM的几年里,劳动生产
率提高了50%,设备综合效率从64.7%提高到82.4%,设备故障率降
低了70%。加拿大WTG汽车公司在推行TPM的最初三年时间里,其
金属加工线每月故障停机时间从10h降到2.5h;生产线废品减少68%,
人员减少一半。
意大利一家公司推进TPM的三年里,生产率提高33.9%,机器故障减
少95.8%,局部停机减少78%,润滑油用量减少了39%,维修费用减
少17.4%,工作环境大大改善,空气粉尘减少90%。实践证明,推进
TPM会提高企业运营能力。
|