为了应对这种挑战和要求,加强设备管理,减少设备故障,延长设备寿命,促进设备运行环节的降本增效就显得尤为重要。那么,设备运行环节怎样才能做好降本增效呢?
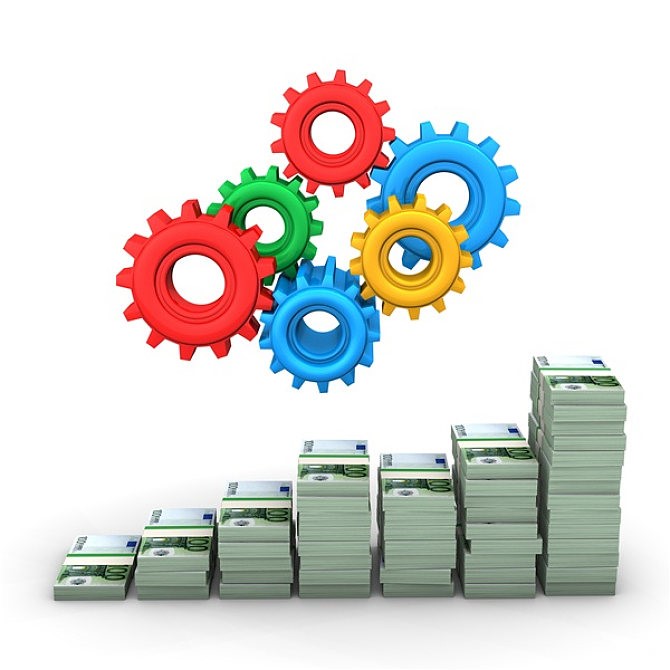
“设备不发生故障就是对成本管理最大的贡献,保障设备正常生产就是设备管理最好的降本增效”。
这一句话非常经典,设备运行环节的降本增效,当务之急就是减少设备故障工时,尤其是要减少设备恶性停机事故,企业一旦发生突发恶性停机事故,就必然严重影响正常生产,设备不能正常生产就是设备管理最大的损失成本。
减少设备恶性停机事故,我们有很多很多的方法和措施,如按照TPM管理的自主保全七步骤和专业保全七步骤做好设备维保,我们还可以完善设备故障分析报告,健全设备维修标准与设备部门周报月报制度,做好设备劣化复原改善,建立专业维修工技能培养机制。
真正设备管理做得好的企业,设备部门是时时维护设备,而不是时时维修设备。
我们不少设备维修工,只能算作换件工,设备坏了,他们就去更换零部件,不去分析设备故障发生的原因,也不做设备预防保全。有些企业,没有设备管理,只有设备维修;设备管理部门不管理,不预防,只抢修;他们用落后的设备管理理念和落后的管理方法去管理最先进的集成自动化设备。
我们必须明白,事前维护比事后维修的损失成本要低得多。
三流维修工,能够快速修理好设备;二流维修工,能够通过设备维护保全减少设备故障;一流维修工,能够通过技术的改造减少设备能耗与提升设备效率。这一句话是颇有道理的。
有些企业设备故障了,设备管理部门的人员却并不着急,他们对设备的恶性停机也不重视,原来是因为公司订单不足生产线没有满负荷生产,设备故障没有影响到交货进度,这台设备坏了他们就调整到另一台设备上生产,在没有满负荷生产的背景下,掩盖了设备恶性停机的巨大损失。
一旦设备发生恶性停机事故,我们应该采取“先止血,后疗伤”的策略减少设备停机的的损失。所谓的“先止血”就是快速抢修好设备,优秀的企业在设备抢修上有个321法则就非常值得借鉴,321法则指的是:设备维修工3分钟赶到现场(3分钟能够赶到现场,说明他们本身就在生产现场);20分钟解决故障(20分钟能够解决故障,说明平时做好了设备维护,没有大的设备故障;20分钟必须解决故障,说明企业对设备故障抢修容忍的极限);1次性调试合格(不能因为设备故障而生产出不良品,用故障修理后的产品合格率来衡量设备维修的效果)。
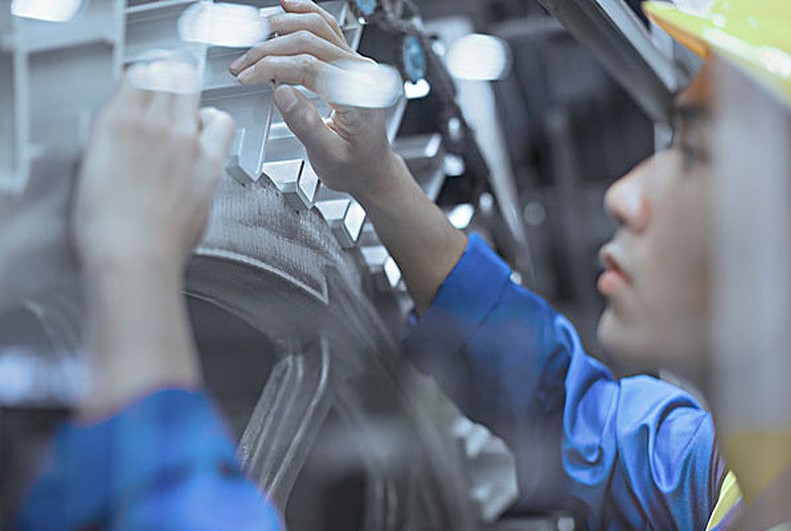
那么,“后疗伤”则要求企业员工向设备故障学习保全,学习正确的设备操作方法。每次故障都是一份改善礼物,每次检修都是一次实战训练。对于典型故障,要依据倒查断根的原则,组织生产管理人员、设备维修工、设备操作工一起互动讨论,分析事故的起因是什么?以前为什么没有发现隐患?其他同类问题是否还存在?预防措施是什么?以前的检修走了什么样的弯路?互动式讨论既分析了故障原因,也培训了员工,尤其是技能差的员工和新员工经历过这种实战培训后能够迅速提升其设备维保的技能,效果是十分明显的。
减少恶性停机的损失,生产部门的员工需要做好设备自主保全,只有生产部门员工通过自主保全做好了防止设备劣化的工作,设备管理部门才能在此基础上做好专业保全;也只有这样,才能够有效发挥专业保全的威力,才能够有效减少设备故障。
|